Modification of Agilent/HP 6644A PSU: Installation of banana connectors in the front panel (feat. DeLucaLabs)
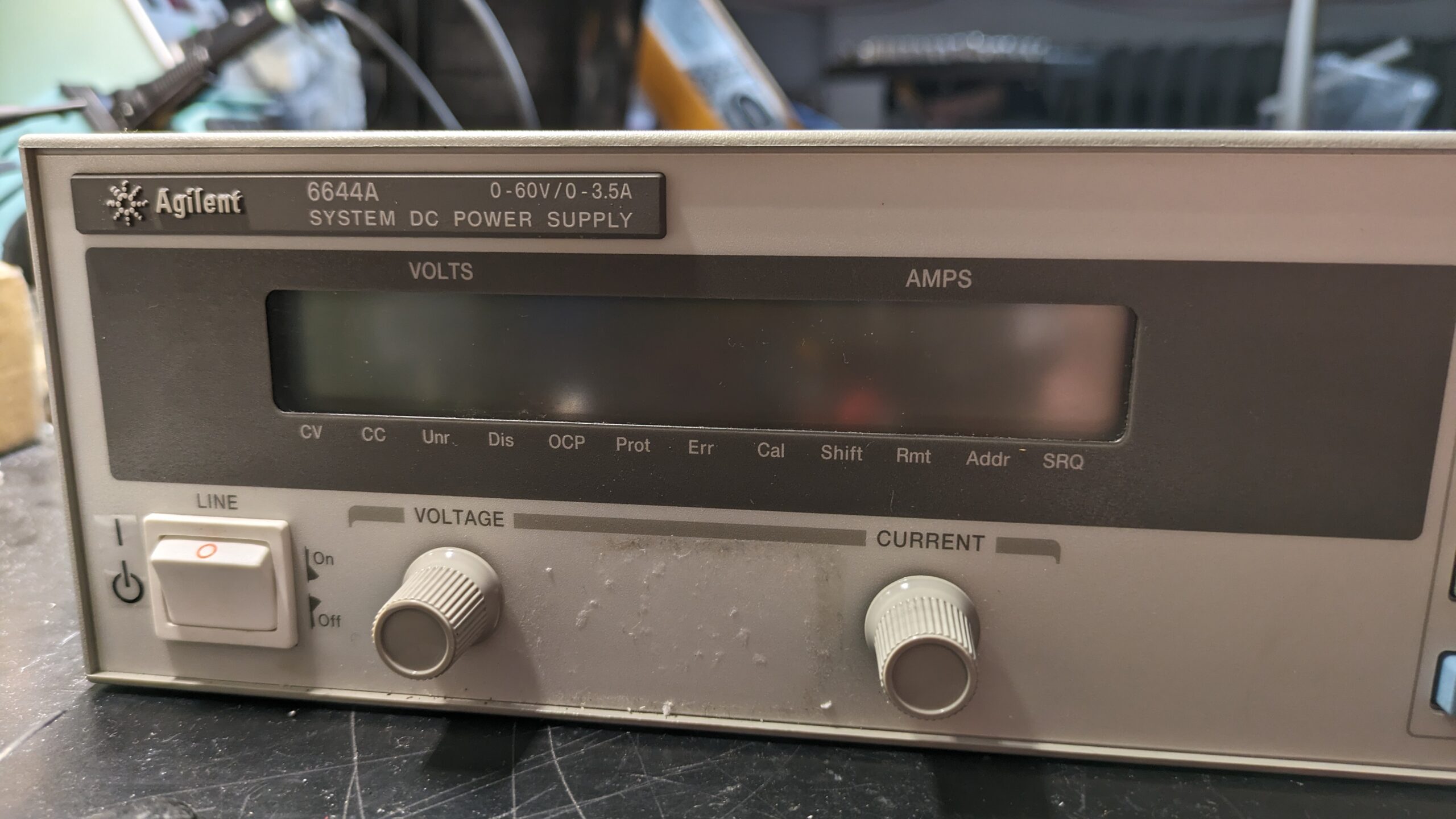
Welcome back to the Klinkon Electronics blog. Today we are going to talk about how to modify HP and Agilent's 66xx series variable power supplies in order to turn them into bench power supplies.
Introduction
The Agilent 6644A linear power supply is a laboratory-grade DC power supply that provides a range of specifications and performance comparable with modern products, if not even better, such as an interface system via GPIB, push-button control for fine-tuning the output (which in our model allows up to 200W with outputs from 0 to 60V/0 to 3.5A) and remote sensing for compensating the voltage drop across the cable.
It is therefore still a very up-to-date product, despite the fact that it was produced in 2003, and for around 200€ you can find it on second-hand markets or at electronics fairs.
The product is designed for use in servers and racks, so there are no classic banana plugs on the front of the unit, but only screw connectors at the rear, which makes them not very 'convenient' for use in the lab, especially considering that the unit in question is designed for front connectors. Today we will perform just the operation of adding these terminals and wiring them into the motherboard.
Connector installation - PCB modification
The installation of the connectors on this model of power supply in itself is not too complex a procedure if one masters a bit of electronics and manual dexterity, since the device shares with other models of the same series the hardware and chassis layout with regard to the outputs, and Hp, the manufacturer of the power supply, had foreseen this possible need and sold an option to have them installed at the factory. (Not to mention that everything is well documented in the "Service Manual", published by the manufacturer itself and freely available online. at this link!)
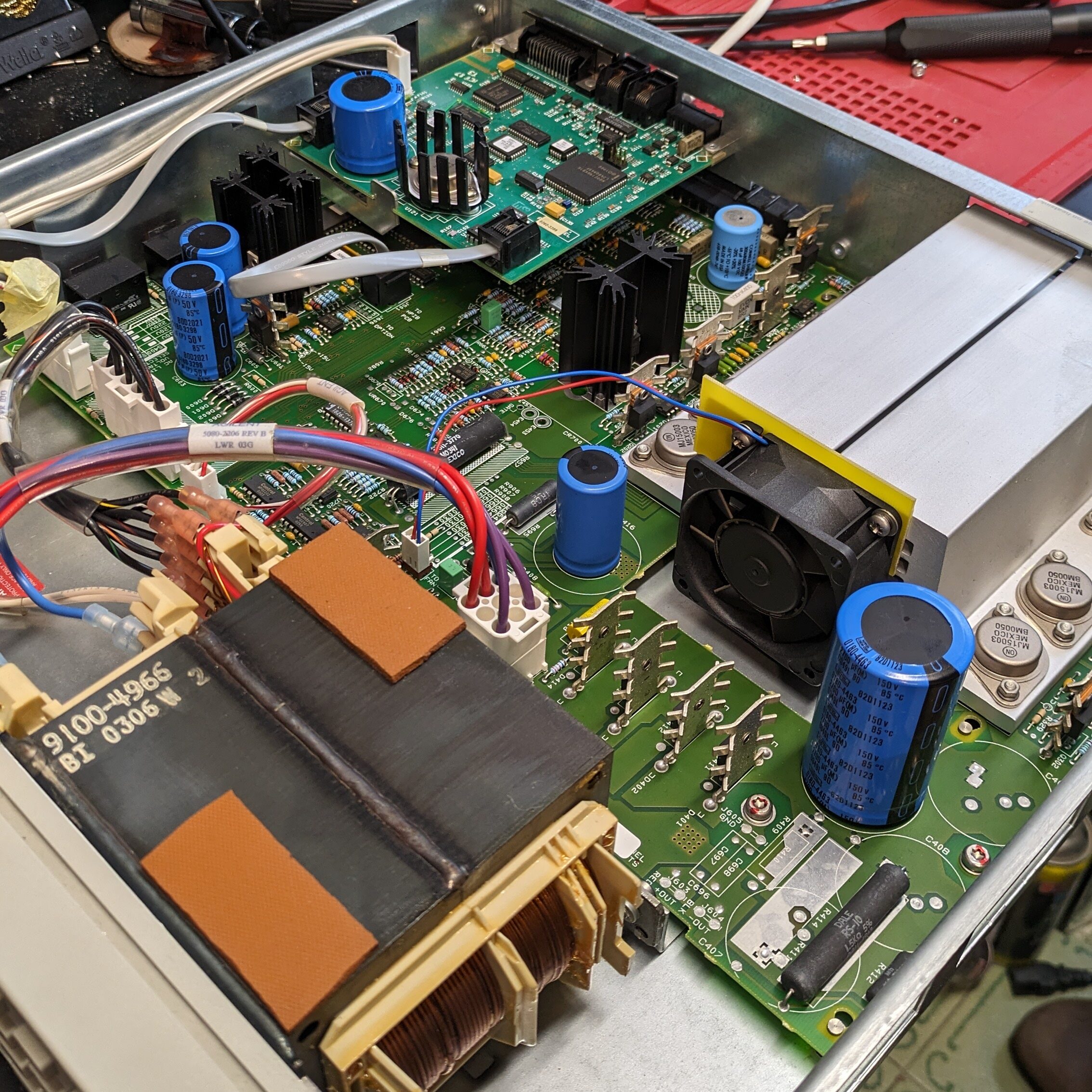
After this introduction, let's get into the action. The PCB is already equipped with the pads to carry the regulated voltage (by soldering three 0 Ohm resistors), the pads for the sword connectors, and the front plastic is already pre-drilled under the adhesive for the installation of the connectors. The circuit board does not provide for voltage sensing signals on the front panel, which remain connected to the rear terminal, although this can be circumvented with external sensing. A non-invasive method that can be applied is to use the external sensing terminal and connect with a clamp two wires from the rear contact to the front connectors via the inside of the device itself, a solution that we discarded, as we want to keep the external outputs as free as possible with a view also to having fewer flying wires inside our device.
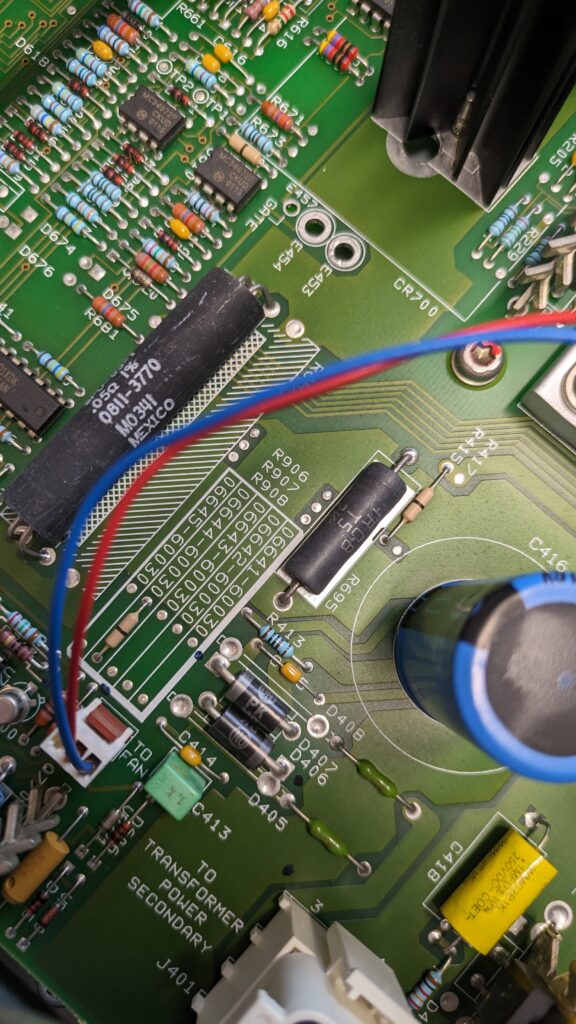

We then set up the power supply to use external outputs by soldering two jumpers, equivalent to 0 Ohm resistors, on pads R906 and R907 (see photo above and below), taking care not to short circuit, and, using the DeLucaLabs air soldering iron, prepare the pads where we will install the sword terminals
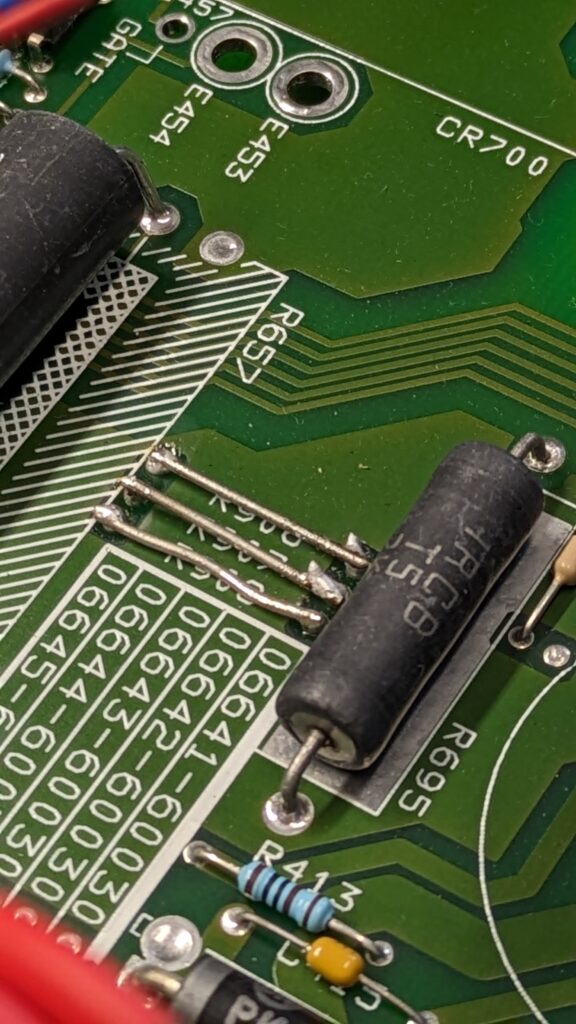
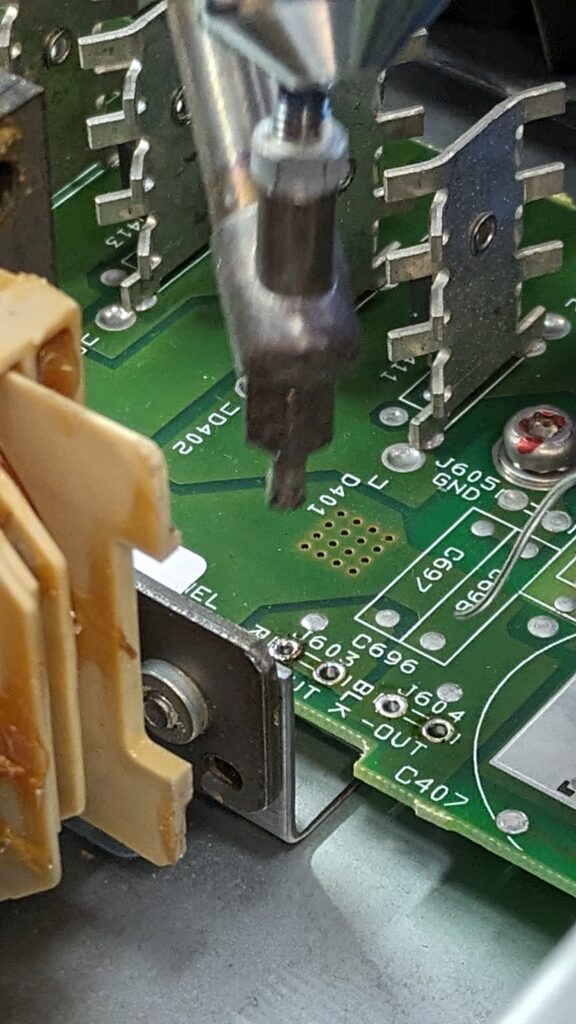
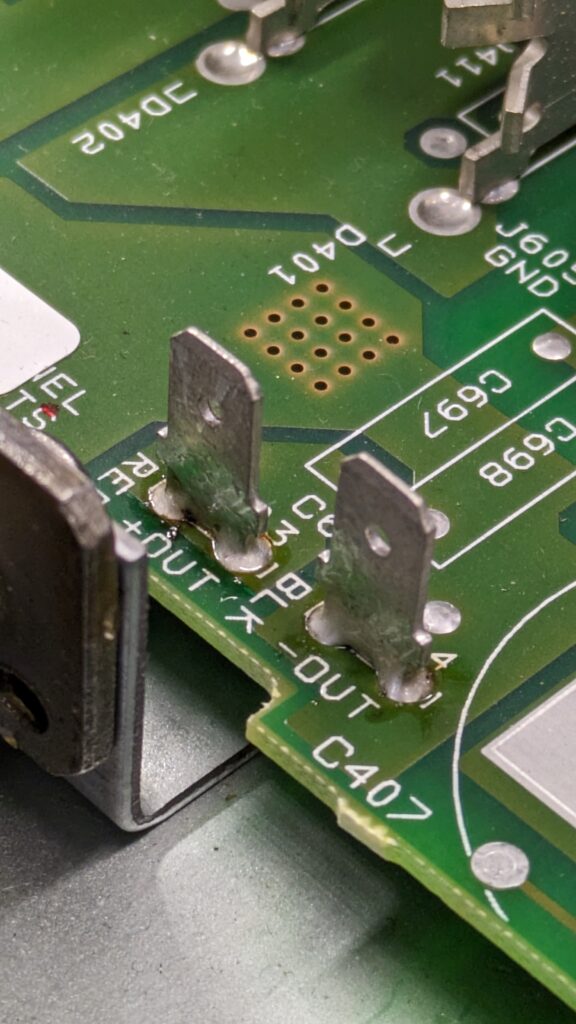
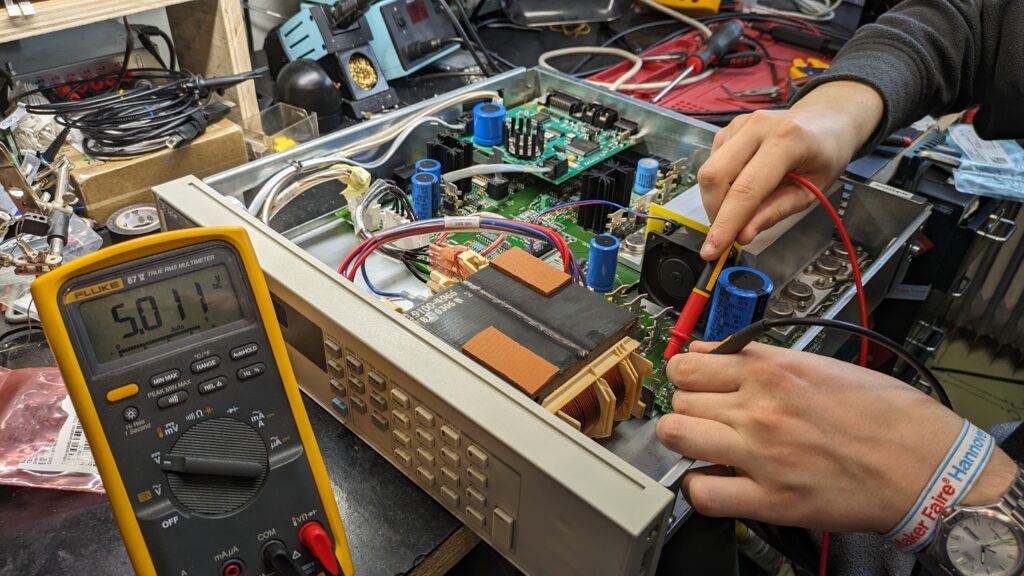
Installation of connectors - front panel modification
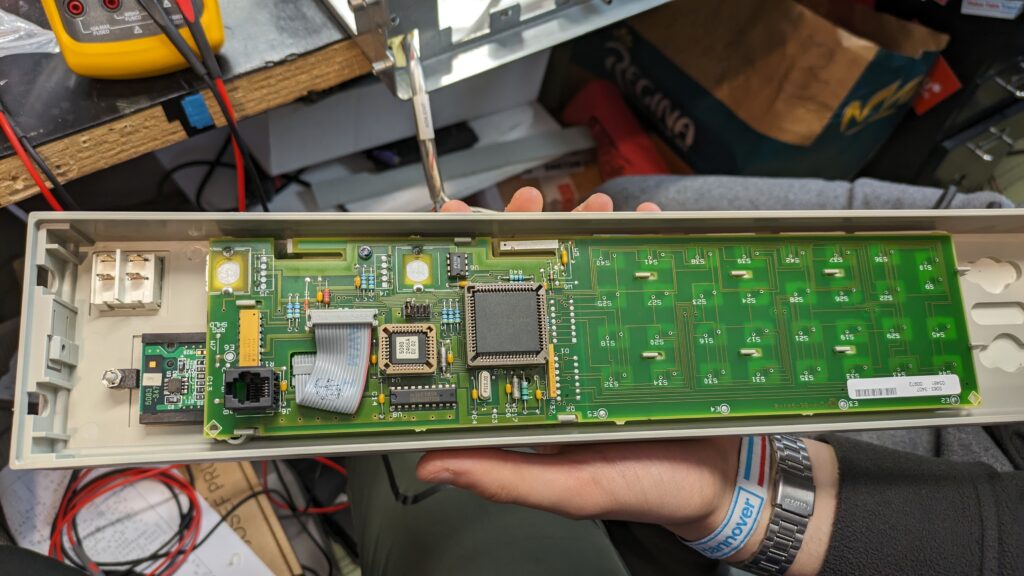
The final steps to get the job done are to install and crimp the connectors to the front panel. We can see on the right the recesses in the plastic, which, as mentioned earlier, are specially placed for models that have the outputs on the front (HP had it right in 2003).
To carry out the modification, therefore, we will need a dremel to drill the front plastic and a small 3D printed piece, so that we can position and fix the clamps (of which we leave a link at the end of the guide)
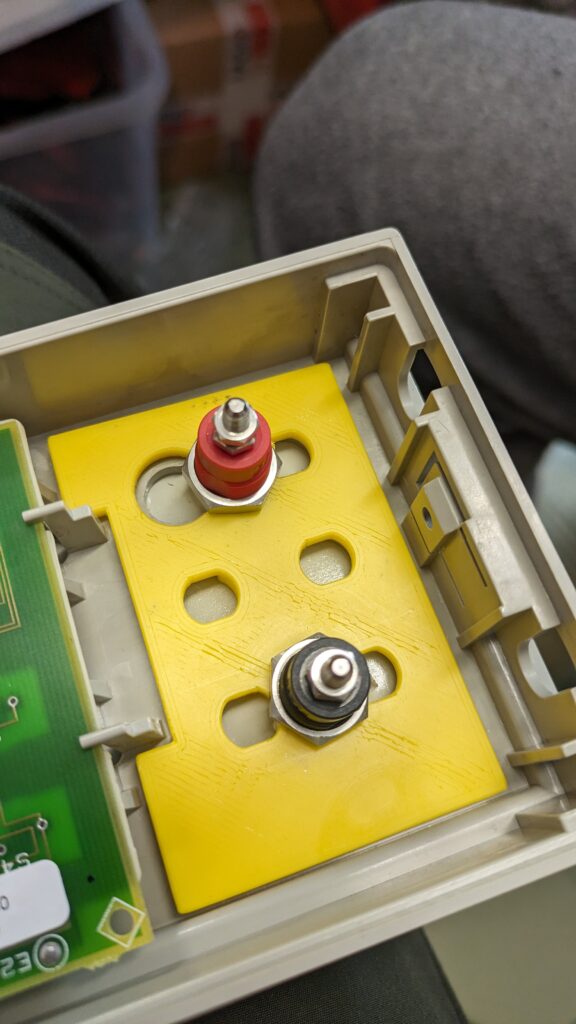
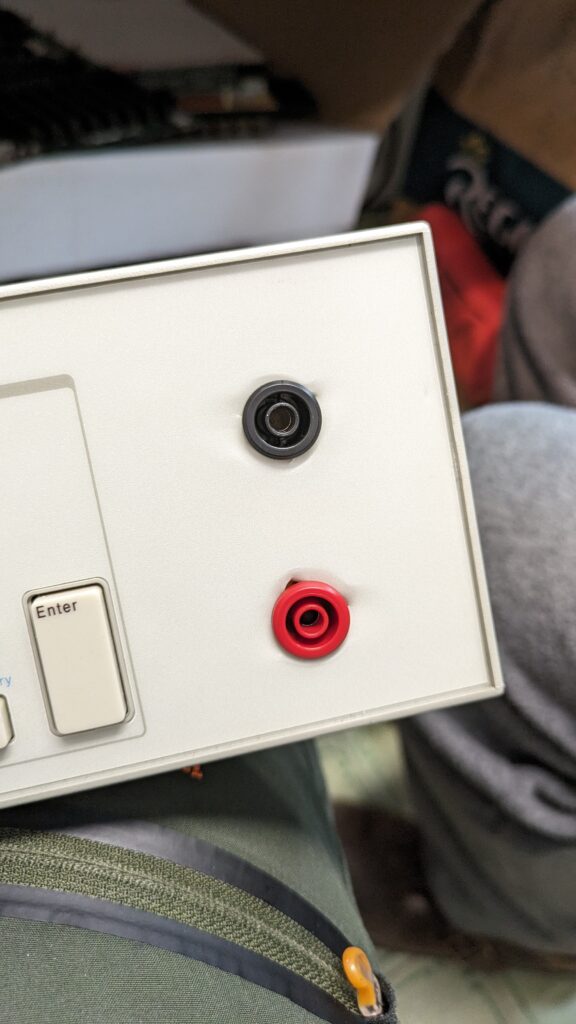
Now all you have to do is install the cables (after prior crimping) between the newly installed terminals and the sword terminals placed on the PCB earlier, and wire the remote sensing from the rear connector to the newly installed one.
Remote sensing is a very important functionality for the power supply, as it allows the voltage drop of the material along the wire to be balanced, and to have exactly the required voltage at the ends of the front connectors.
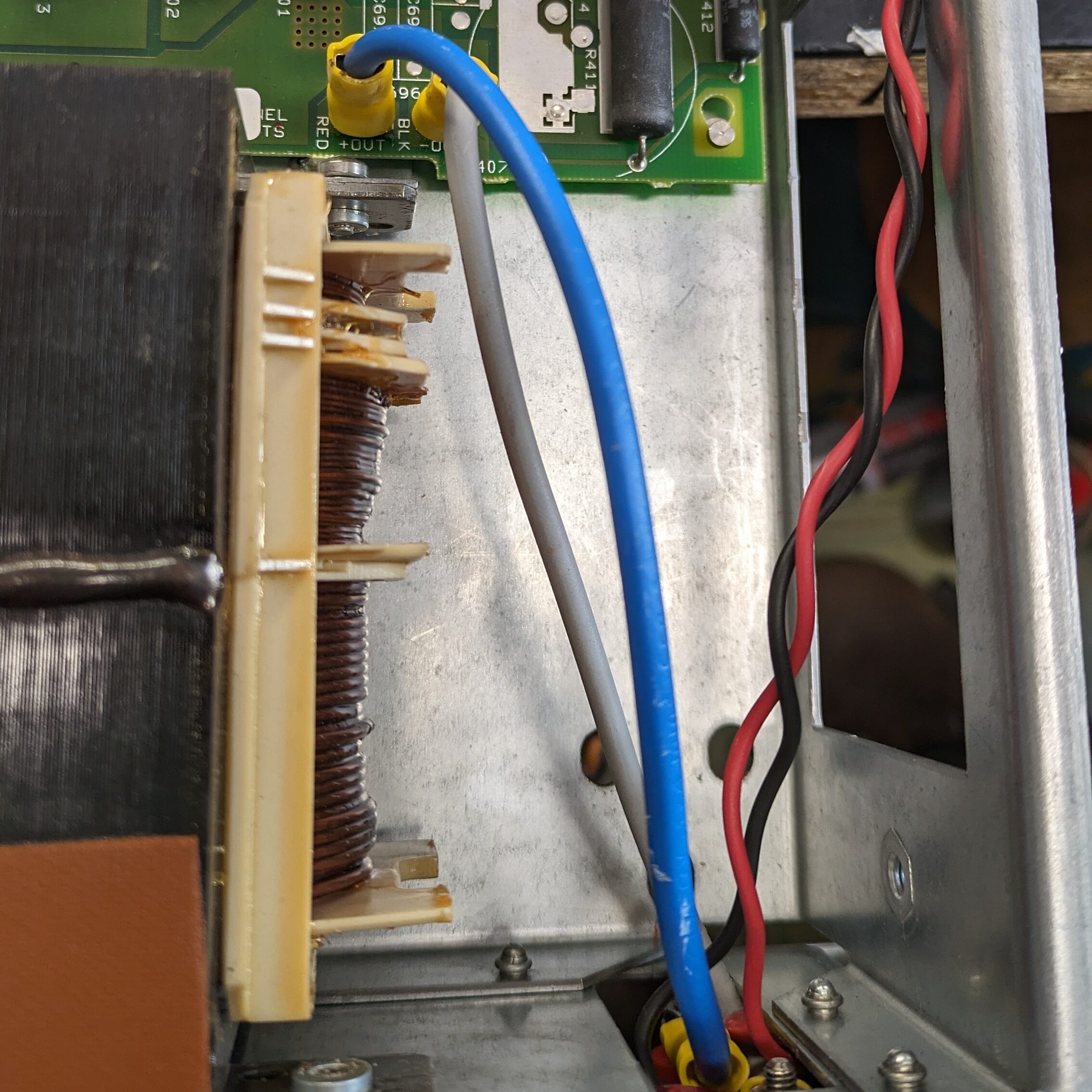
We can now move on to reassembling the power supply and after a functionality test the procedure can be said to have been successfully completed!
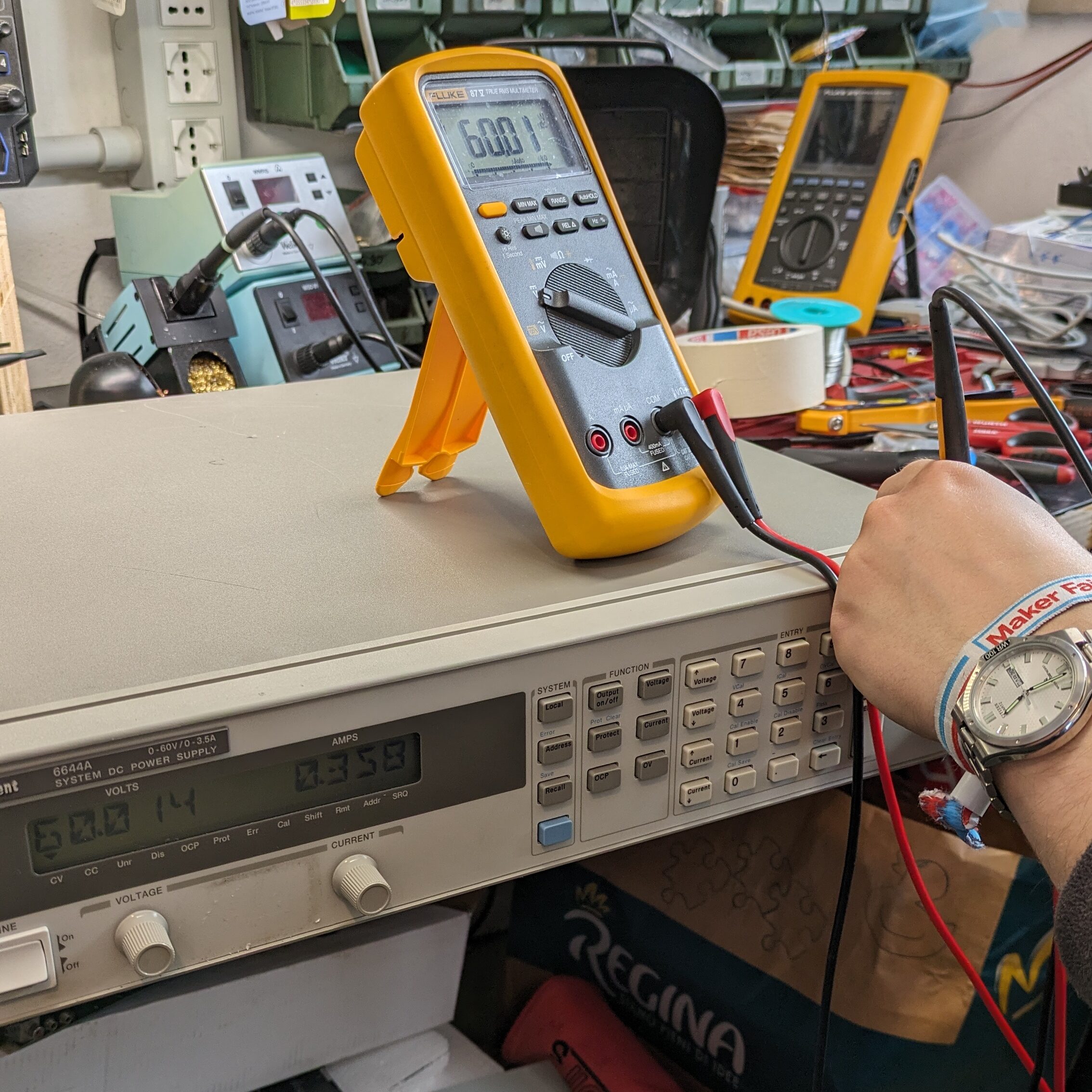